在塑料加工领域,PVC挤出机的高效运行直接决定了产品质量与生产效率。然而,许多操作人员在实际生产中常因参数设置不当,导致产品出现表面粗糙、尺寸偏差甚至设备损坏等问题。掌握温度、螺杆转速、压力等核心参数的调节技巧,不仅能提升成品率,更能延长设备寿命——这正是每位工程师必须精通的”基本功”。
一、温度控制:挤出工艺的”生命线”
PVC材料的加工特性决定了温度敏感性。挤出机通常分为进料段、压缩段、熔融段和均化段,每个区域的温度设定需遵循”梯度升温”原则:
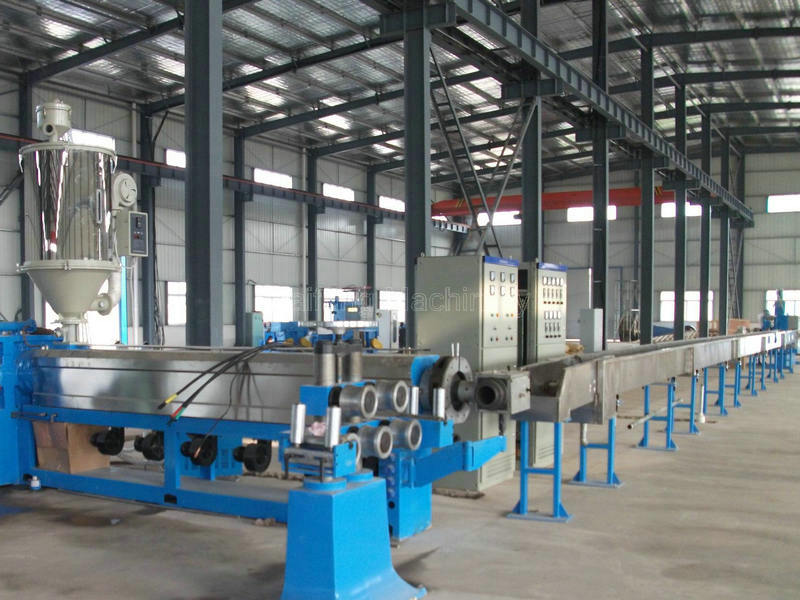
- 进料段(160-170℃):温度过高会导致原料过早塑化堵塞进料口,温度过低则影响输送效率
- 熔融段(180-190℃):此阶段需完全熔融PVC颗粒,温度波动超过±3℃即可能引发分解反应
- 模头段(175-185℃):适当降温可稳定产品定型,但需与冷却系统形成协同效应
典型案例:某管材生产企业通过将均化段温度从195℃降至185℃,成功将气泡缺陷率从12%降至1.8%。
二、螺杆转速:速度与质量的平衡艺术
作为挤出机的心脏部件,螺杆转速直接影响产量与塑化效果。调节时需注意:
- 转速与温度联动:每提升10rpm,熔体温度可能上升2-3℃,需同步调整加热系统
- 背压控制:保持0.5-2MPa背压可提高塑化均匀性,但超过3MPa会加速螺杆磨损
- 产量公式:Q=πD²hN/4(D螺杆直径,h螺槽深度,N转速)可作为理论参考值
黄金法则:对于φ65mm螺杆,生产3mm壁厚管材时,建议转速控制在25-35rpm区间。
三、模具压力:决定产品精度的”无形之手”
模头压力调节常被忽视,却是影响产品尺寸稳定性的关键因素:
- 压力监测:安装熔体压力传感器(建议量程0-40MPa)
- 调节技巧:
- 通过口模平直段长度调整:每增加10mm长度,压力提升约15%
- 采用阻流块微调:可改变局部熔体流速分布
- 预成型板优化:将开孔率控制在60-70%可平衡压力与流速
某型材生产企业通过优化模具压缩比(从3:1调整为2.5:1),使角线接缝问题减少70%。
四、冷却系统:容易被低估的关键环节
冷却效率直接影响产品结晶度和机械性能:
- 真空定径箱水温建议控制在12-18℃,温差需稳定在±1℃以内
- 喷淋冷却角度应调整为45°入射,确保管材周向均匀冷却
- 牵引速度匹配公式:V=Q/(ρ×A)(Q挤出量,ρ材料密度,A截面积)
注意:过快的冷却会导致内应力积聚,建议采用”梯度降温”法,第一段冷却水温比后续段高5-8℃。
五、参数联动:系统化调整策略
挤出工艺本质是多参数耦合系统,建议建立以下调整流程:
- 根据配方确定基础温度曲线
- 以60%额定转速启动设备
- 观察熔体压力波动是否在±5%范围内
- 通过在线测径仪实时反馈调整牵引速度
- 每调整一个参数后,需稳定运行15分钟再记录数据
某薄膜生产企业通过引入MES系统,将参数调整时间从3小时缩短至45分钟,废品率降低40%。
六、常见问题快速诊断表
现象 |
可能原因 |
解决方案 |
表面鲨鱼皮 |
熔体温度过低 |
提升模头段温度3-5℃ |
轴向条纹 |
螺杆转速过高 |
降低10-15rpm并检查滤网 |
截面椭圆 |
冷却不均匀 |
校准真空箱水位与喷淋角度 |
颜色发黄 |
局部过热分解 |
检查加热圈接触与热电偶精度 |
掌握这些核心参数的调节逻辑,就能让PVC挤出机从”能用”变为”好用”。随着智能控制技术的普及,参数优化正从经验驱动转向数据驱动,但基础原理的深刻理解始终是技术升级的基石。